SP 2 Intelligent lightweight design through multi-component processes
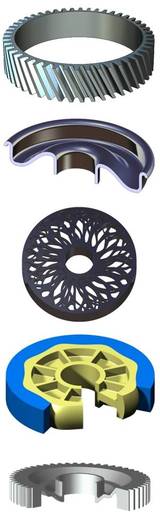
(P 1056 / Pre-Competitive Cooperative Industrial Research Project (IGF) No. 18189 N) FZG, IWT, IFU, UTG
Subproject 2 of the “massiverLEICHTBAU” (Lightweight Forging) joint project, funded by the German Federation of Industrial Research Associations (Arbeitsgemeinschaft industrieller Forschungsvereinigungen – AiF) and the Federal Ministry for Economic Affairs and Energy (Bundesministerium für Wirtschaft und Energie – BMWi), is being worked on as collaborative research program under the management of the Gear Research Centre (Forschungsstelle für Zahnräder und Getriebebau – FZG) of the TU München. The cooperating institutes are as follows: the Institute for Metal Forming Technology (Institut für Umformtechnik – IFU) of the University of Stuttgart, the Foundation Institute of Materials Science (Stiftung Institut für Werkstofftechnik – IWT) and the Institute of Metal Forming and Casting (Lehrstuhl für Umformtechnik und Gießereiwesen – utg) of the TU München.
The weight of powertrain components has been continuously reduced by load-adapted design and through the materials savings achieved by this in regions with low stress. With the consistent increase in the power density and the associated reduction in weight, additional potential is available for the intelligent lightweight design of powertrain components in future. Significant potential is offered by taking an integrated look at part design, material, heat treatment as well as the production and joining processes used. By combining various production processes and materials, the different requirements placed on various component areas are fulfilled in a targeted way. This enables lightweight design which is adapted to the part load and is cost-efficient.
On the basis of multiple component design, solutions are worked on to incorporate individual forged components in entire structures. The use of higher-strength components made of steels with increased load-bearing capacity and optimized heat treatment operations generates additional application fields for forged parts. High power density and low part weight are achieved with gears designed with the use of a high-strength steel for a gear rim with highly loaded splines. This gear rim is combined with a wheel body in lightweight design. The wheel body can be produced from ultra-high-strength sheet materials with very low weight. Through deep drawing, very light wheel bodies with thin wall thicknesses are attained. Furthermore, stacking of blanked sheet parts yields a weight saving due to a load-optimized wheel body structure (utg). Producing wheel bodies by means of forming allows the positive- and/or friction-connected joining of gear rim, wheel body and shaft, thereby enabling a compact, weight-optimized design (IFU). The thermal joining of a press fit between the case-hardened gear rim and wheel body can be achieved efficiently through specifically exploiting temperature differences directly during the quenching process (IWT). Selected prototypes are being analyzed with respect to functional behaviour and durability (FZG).
The advantage of such a design (differential design) compared to an integral one lies in the ability to combine optimized processes for generating individual components with a load-adapted design. By using processes geared to individual parts, the relevant operations are optimized without having an unwanted effect on other components, such as the case would be if integrated heat treatment were used.
The insights gained in this way into material selection, production technology as well as the functional and service life behaviour contribute to a deepened understanding of assembled gears and serve as supportive guidelines when designing such gears for various applications.